We’re at Toronto Pearson International Airport, going behind the scenes to discover what it takes to be an AC station attendant. Join us as we flex our muscles, power up a Boeing 777, and send over 3,000 kgs of live lobster to Hong Kong. Are you ready? Our journey begins on Pier LF 2-3, where passenger luggage is arriving for flight AC 015 en route to Hong Kong. The pier is managed by conveyor belts, and as we follow a piece of luggage on the top conveyor belt, we are reminded to wrap all valuables with care. Each bag is scanned for its identification and destination. Over the course of one shift, a team may load between 4,000 and 6,000 bags.
We received a call from AC Operations Stock Center, which is responsible for the management of all airside operations. A Boeing 777 was parked overnight just outside the AC hangars and needed to be powered out before being towed to its departing gate. We quickly jumped on board to help tow crew station attendant Craig gets the job done. The APU provides electrical power and also runs hydraulic pumps, and it took roughly 5 minutes to start the plane’s APU.
Meanwhile, back at Pier LF 2-3, the baggage team had sealed up the last of flight AC 015’s containers and attached them to a baggage tractor. Loading these containers onto the plane is an art in itself, and lead station attendant Mike and his crew had just under 30 minutes to load both the nose and tail cargo holds. Using a load sheet, the team loads containers according to their tight weight and dimension, optimizing the plane’s balance and efficiency.
Mike and his crew began to load the front cargo hold with heavy commercial goods, to prevent the plane from tipping backwards due to excess tail weight. The 3,000 kg pallet of live lobster was the last of the commercial goods to be loaded, but with a little extra muscle and the help from hundreds of robotic wheels, the crew was able to load the pallet with ease.
With moments to go, we received another call from stock, informing us that a bag needed to be transferred from an arriving flight to a connecting flight. Young AC station attendant Nelson was able to meet the plane at its gate, locate the bag, and deliver it to its connecting flight.
Back at flight AC 015, Mike and his crew had just finished loading the passenger cargo and were now ready for pushback. Planes cannot reverse, so a pushback tractor is needed to push the plane to a point where its engines can power it forward to the runway. Mike pushed the plane into position, the tow bar was released, and the communication cord was disconnected. With the tractor at a safe distance, the pilots were given the final signal to taxi to the runway.
Within minutes, the plane was ready for takeoff and over 50 tons of commercial and passenger cargo were on their way to Hong Kong. Thanks for joining us on this quick behind-the-scenes tour through Air Canada’s baggage and ramp operations.
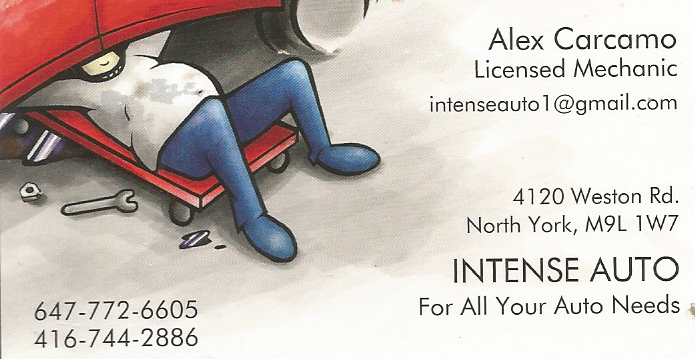